Services
PCB Assembly (PCBA)
PCBA is a synergistic process, in which the whole comes to life after assembling its various parts. As your EMS partner, we guarantee a resilient and durable electronic assembly.
Since the beginning, PCBA has been at the heart of Fox EMS. Over the last decade, substantial efforts were invested to give us access to a horizon of limitless capabilities. Ranging from a simple single-sided assembly, all the way to a complex multi-sided PCBA, the non-exhaustive list below outlines our services.
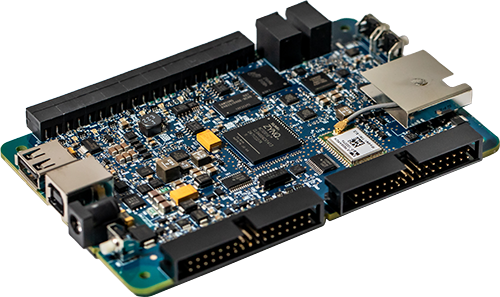
Assembly types
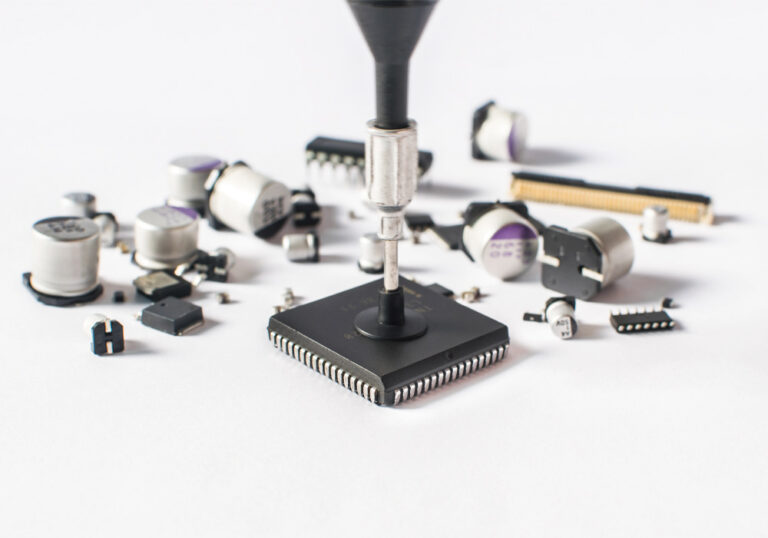
Surface Mount Technology
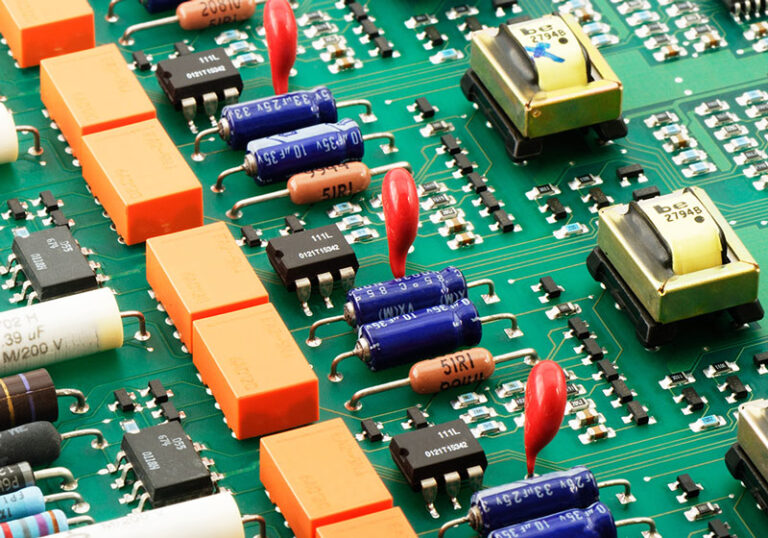
Through-Hole Technology
Components
• Smallest part: up to 01005
• Fine pitch: up to 0.3 mm
• BGA, uBGA, CSP, QFN, QFP, PoP, CoB, etc.
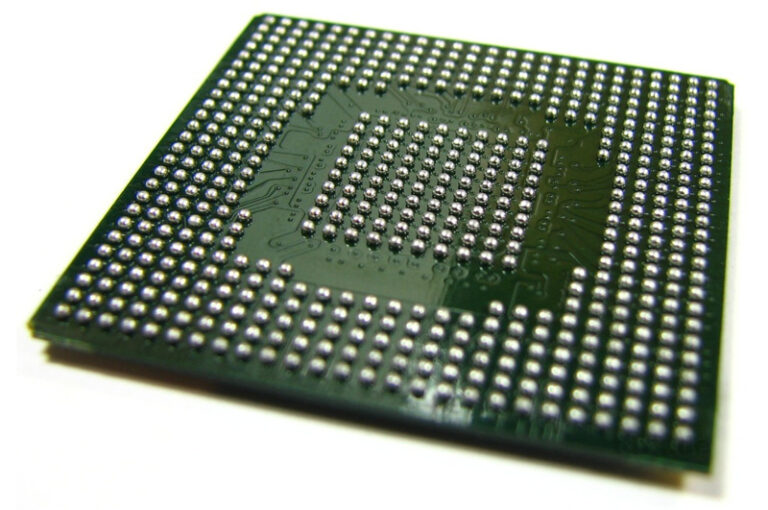
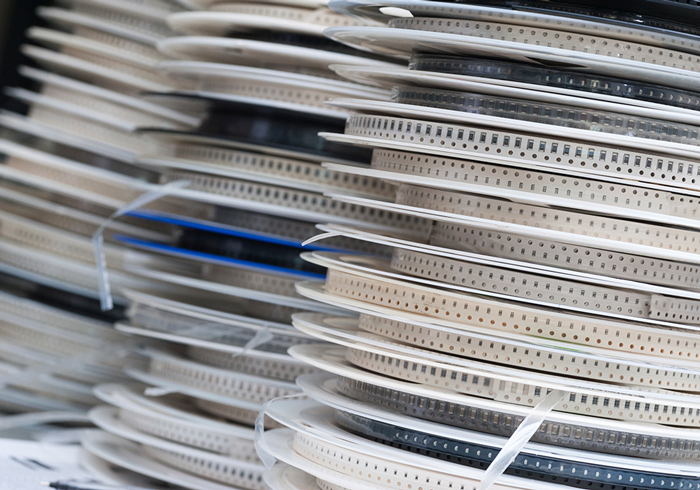

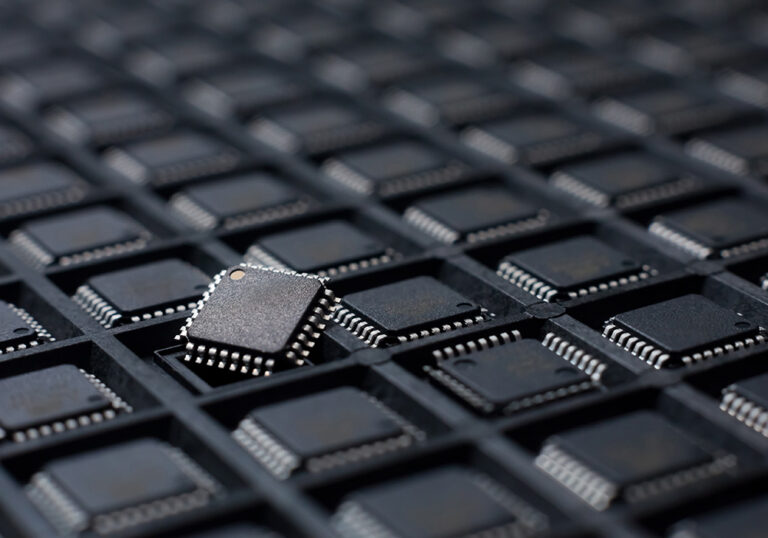
Component Packaging
• Cut tape
• Tube
• Tray
• Partial/Full reel
• Bulk
Soldering
• Reflow oven (Nitrogen and air)
• Wave soldering
• Selective wave soldering
• Soldering robot
• Manual soldering
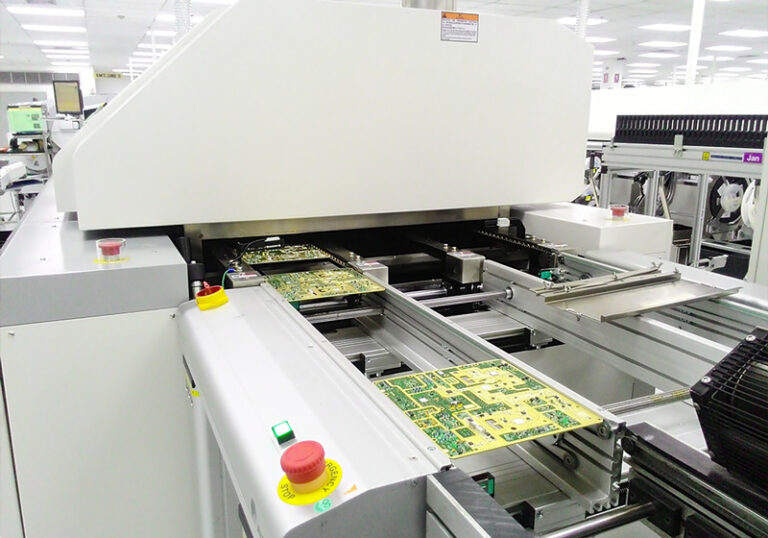
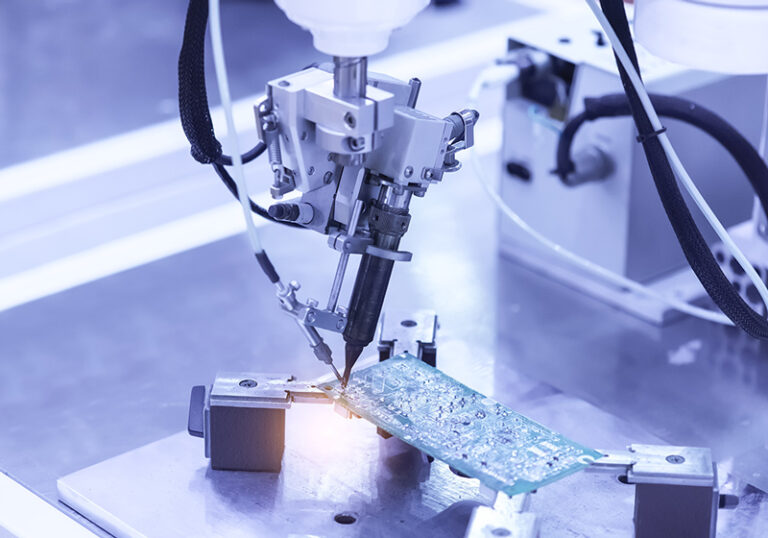
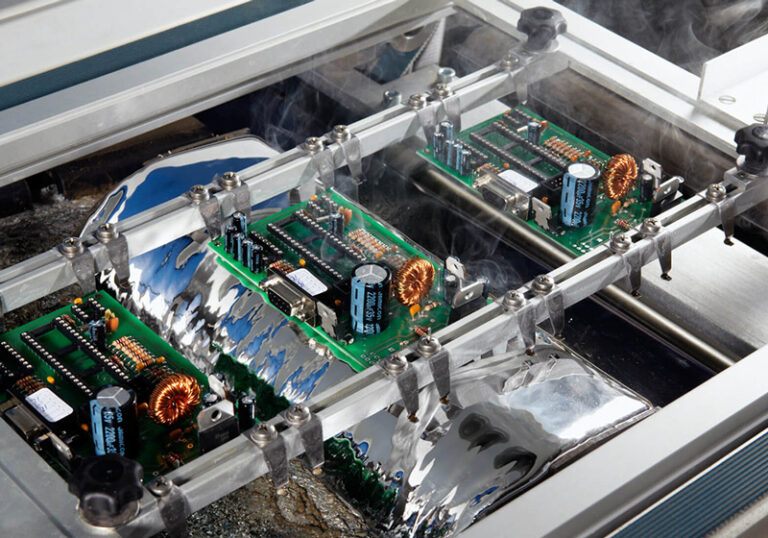
For most of the devices that are used in our daily lives, we follow the IPC Class 2 standard. Such products mainly belong to these markets: Consumer Electronics, IoT, Industrial, Telecom.
We commonly follow the IPC Class 3 and MIL-SPEC Standards for Aerospace, Military & Defense, Oil & Gas, Automotive and Medical projects.
Also known as IC Programming, Firmware Injection, Flashing or Burning. All these are common names for the process where a program is transferred to an Integrated Circuit.
At Fox EMS, this can be done:
• Prior to the assembly, using a specific Fixture/Adapter compatible with the IC Package.
• After the assembly, using a standard communication bus, such as USB, SWD, JTAG, UART, etc. This usually requires a programmer (ST Link, Segger, etc.) and a Cable with a Connector to make contact with a specific part of the board.
To separate the PCBAs from the panel, we use two methods: V-Cut or Milling.
Milling is the preferred method for Automotive, Aerospace, Defense and Oil and Gas, as it does not apply any Stress on the Board.
Potting
Potting is a method that protects the PCBA by encapsulating it with a liquid material (ex: Resin, Polyurethane, Silicone). This material will fill the device’s housing and cover most of the components. Once solidified, this material will act as a protection against impacts, shocks, heat, chemicals and other environmental hazards.
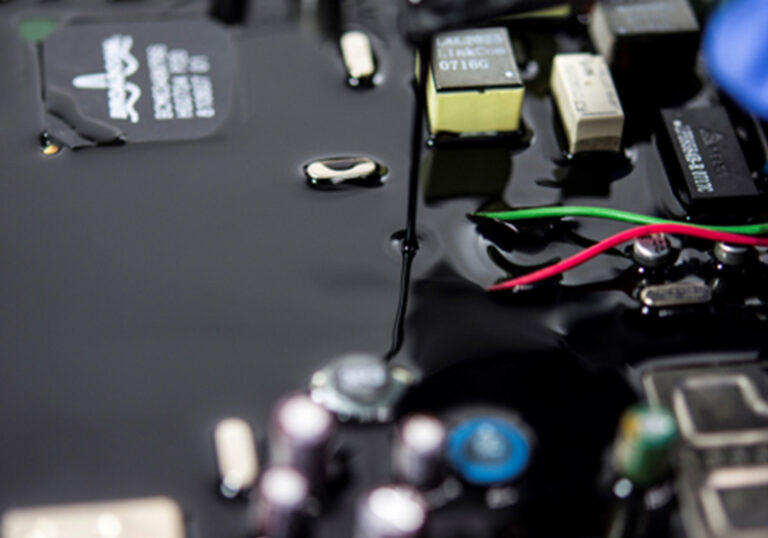
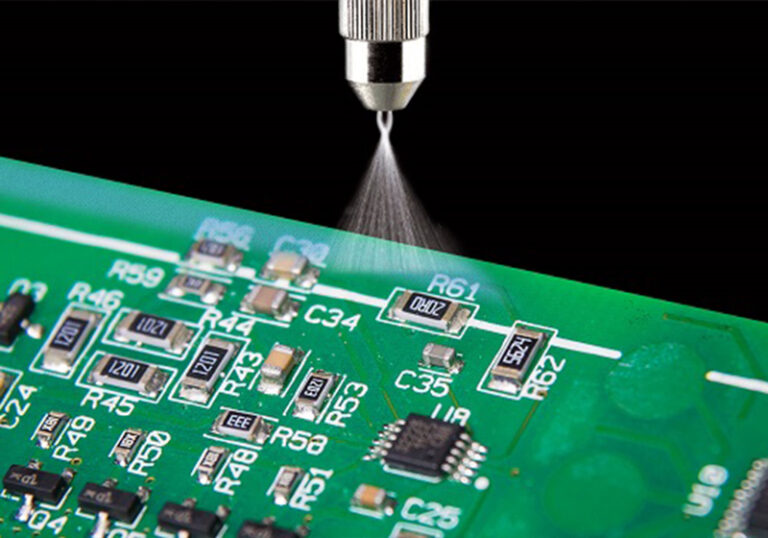
Conformal Coating
Printed circuit boards are often expected to perform in various conditions. Conformal coating is another method that protects the board and components against the harsh environment (ex: moisture, hazardous material), thus prolonging its lifespan. This is done by applying a thin layer of polymeric film or another non-conductive material over both sides of the board.
BGA Rework
A BGA rework station is a machine that can be used to repair PCBAs with Ball Grid Array (BGA) components. The station is used to remove the defected parts and re-solder the proper ones.
At Fox EMS, we can also de-solder a BGA component from one board, clean it, “Re-Ball” it and assemble it on another board.
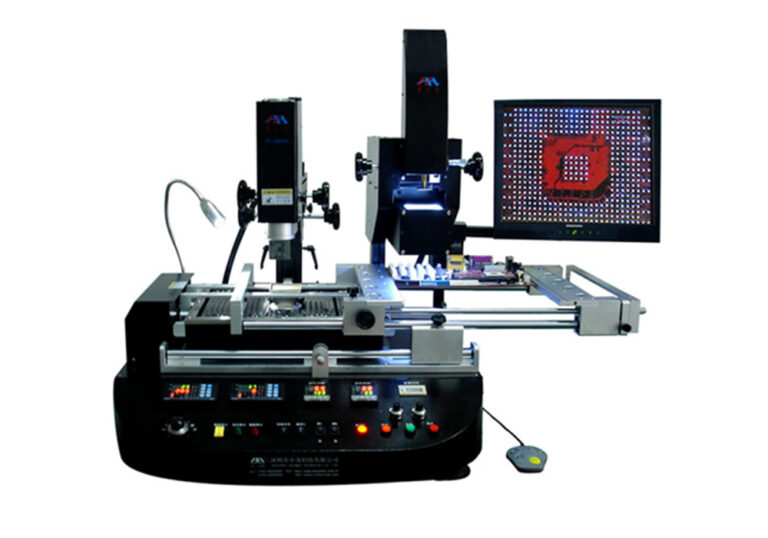
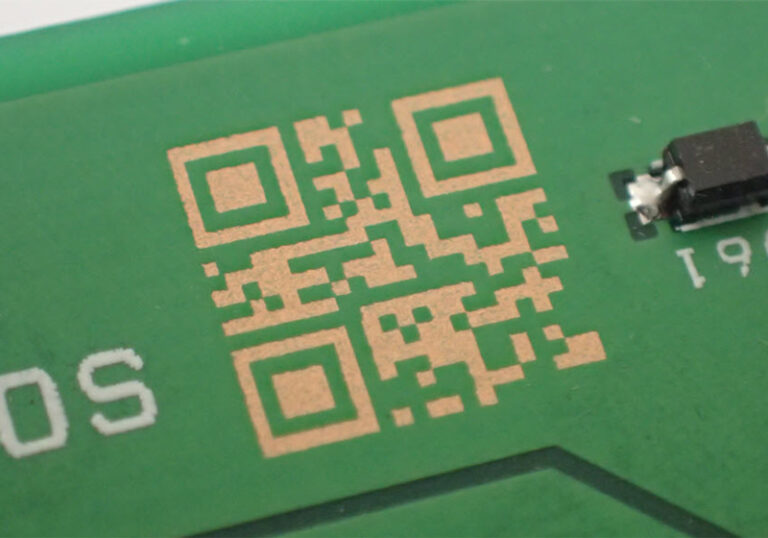
Traceability
Most of our Aerospace, Military & Defense, Oil & Gas, Automotive and Medical projects require a certain level of board traceability.
We can use labels or laser engraved QR codes, to store in the MES software all production steps and components information.
Automated Assembly Lines
• Automatic PCB Loader
• Automatic Stencil Printer
• SPI
• Pick and Place Machines
• Reflow Oven
• Automated Optical Inspection
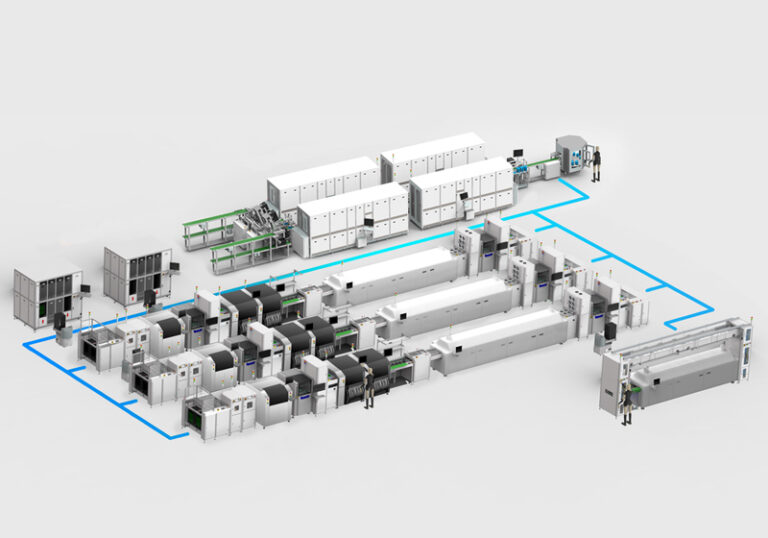